Track rollers
Features
Track rollers LFR are double row angular contact ball bearings comprising an outer ring with a gothic arch profile, an inner ring and two ball and cage assemblies with plastic cages. The inner ring and outer ring are made from rolling bearing steel 100Cr6.
The special outer ring gives two point contact in the contact zone with the raceway, ➤ Figure. The contact angle α is a maximum of 30°.
The bearings can support axial forces from both directions as well as radial forces.
Gothic arch, two point contact, contact angle
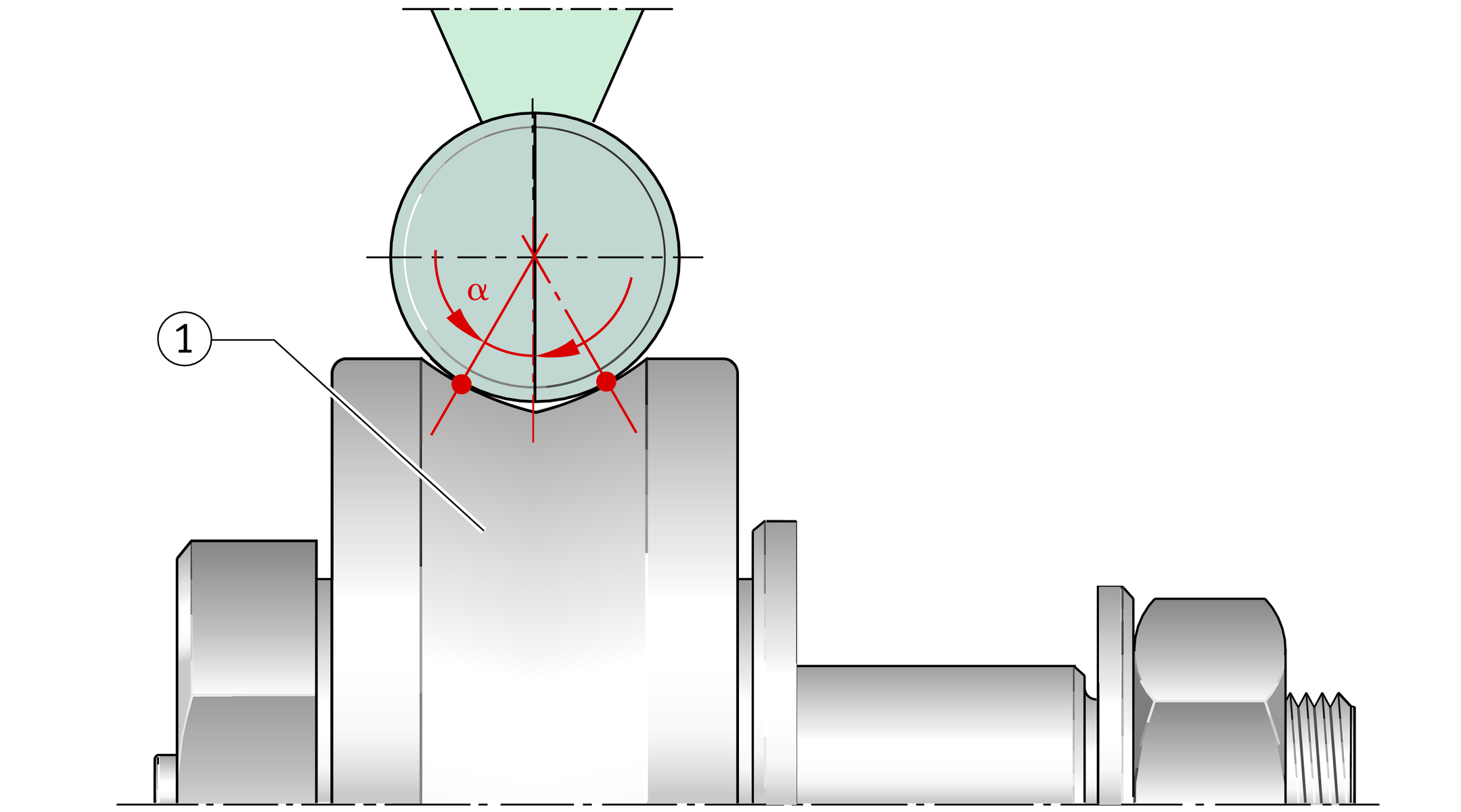

Track roller with extended inner ring
Track rollers LFRI are double row angular contact ball bearings. They differ from track rollers LFR in that they have an extended inner ring. This allows exact positioning in the adjacent construction. The inner ring is mounted by means of a standard screw (for example ISO 4762) in a fit hole (preferably grade F6). The fixing screw is not included in the scope of delivery. The operating clearance of track rollers with an extended inner ring cannot be set by means of eccentric bolts.
Track roller LFRI with fixing screw
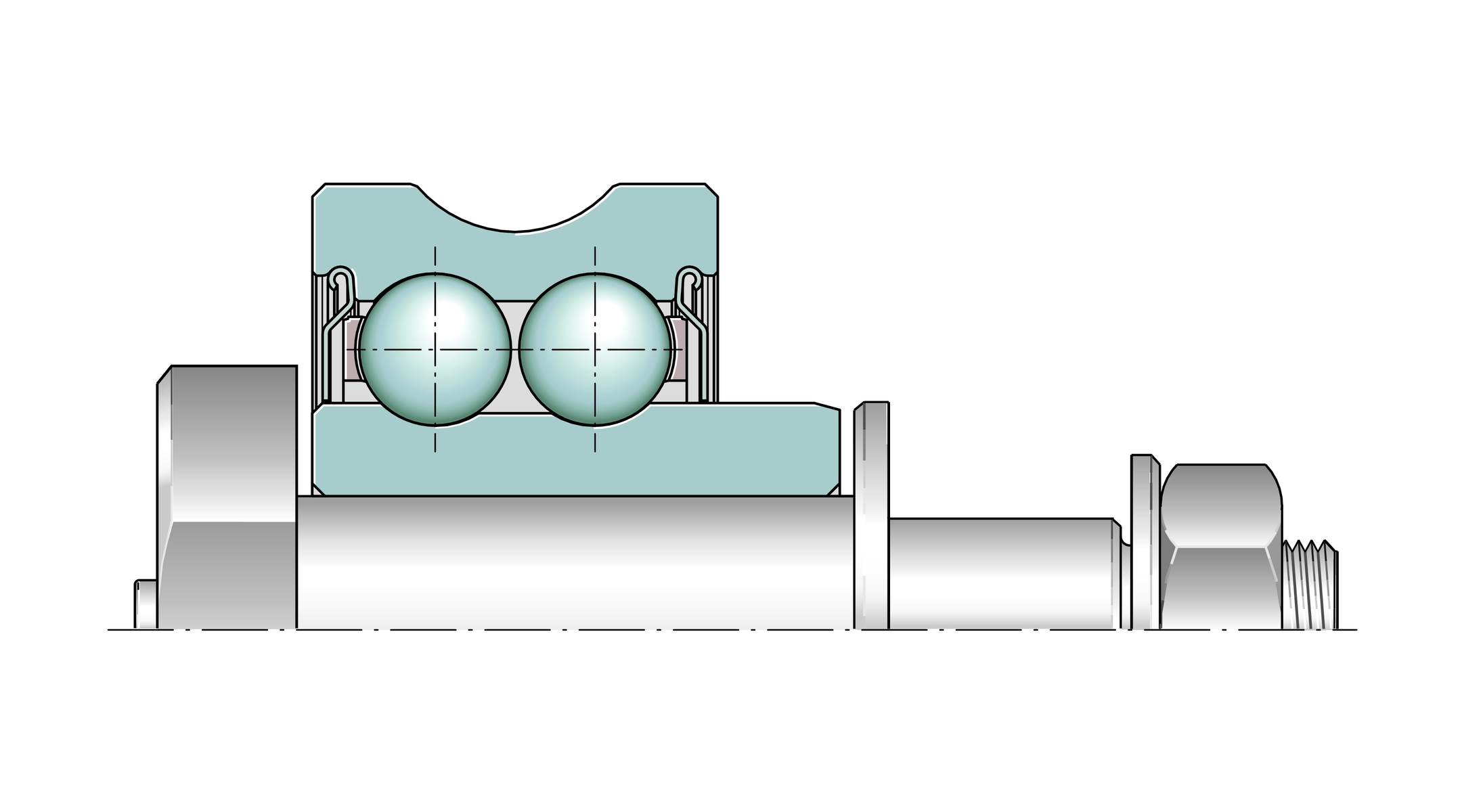
Sealing and lubrication
Gap seals on both sides protect the rolling element system against contamination. Bearings with this seal type have the suffix 2Z.
The track rollers are also available on request with contact seals on both sides, suffix 2RS and 2RSR.
The track rollers are greased for life and are therefore maintenance-free. From outside diameter ≧ 52 mm, the inner ring has a lubrication bore.
Seal types
Seal types and their specific features: see table .
Specific features
2Z seal | |
---|---|
not radially preloaded low friction to be used with low levels of contamination. | |
2RSR seal | |
radially preloaded to be used with higher requirements for sealing action and under heavy contamination. | |
2RS seal | |
axially preloaded to be used with higher requirements for sealing action and under heavy contamination. |
Corrosion-resistant design
The inner ring and outer ring are made from corrosion-resistant steel. The rolling elements are protected against corrosion by the grease.
Corrosion-resistant designs have contact seals and the suffix 2RS-RB or 2RSR-RB.
Accuracy
and internal clearance
The dimensional and geometrical accuracies correspond to tolerance class PN to DIN 620.
The radial internal bearing clearance corresponds approximately to internal clearance group Group N in accordance with ISO 5753-1; internal clearance classes: see Catalogue HR 1, Rolling Bearings.
Possible combinations of track rollers and guideways
The tables show the possible combinations of track rollers with the guideways LFS and shaft and support rail unit TS.
Combinations with guideways LFS
Width and shaft diameter** | Track roller LFR | ||||||
---|---|---|---|---|---|---|---|
LFS | dLw | 50/5-4 | 50/5-6 | 50/8-6 | 5201-10 | 5301-10 | 5302-10 |
20 | 4 | ● | ‒ | ‒ | ‒ | ‒ | ‒ |
25 | 6 | ‒ | ● | ● | ‒ | ‒ | ‒ |
32 | 6 | ‒ | ‒ | ● | ‒ | ‒ | ‒ |
42 | 10 | ‒ | ‒ | ‒ | ● | ● | ● |
52 | 10 | ‒ | ‒ | ‒ | ● | ● | ● |
86 | 10 | ‒ | ‒ | ‒ | ● | ● | ● |
120 | 10 | ‒ | ‒ | ‒ | ● | ● | ● |
●
available size
** Width b and shaft diameter dLw.
Combinations with guideways LFS
Width and shaft diameter** | Track roller LFRI | ||
---|---|---|---|
LFS | dLw | 50/8-6 | 5201 |
20 | 4 | ‒ | ‒ |
25 | 6 | ● | ‒ |
32 | 6 | ● | ‒ |
42 | 10 | ‒ | ● |
52 | 10 | ‒ | ● |
86 | 10 | ‒ | ● |
120 | 10 | ‒ | ● |
●
available size
** Width b and shaft diameter dLw.
Combinations with shaft and support rail units TS
Shaft diameter | Track roller LFR | ||||||
---|---|---|---|---|---|---|---|
dLw** | 5201-12 | 5204-16 | 5206-20 | 5206-25 | 5207-30 | 5208-40 | 5308-50 |
12 | ● | ‒ | ‒ | ‒ | ‒ | ‒ | ‒ |
16 | ‒ | ● | ‒ | ‒ | ‒ | ‒ | ‒ |
20 | ‒ | ‒ | ● | ‒ | ‒ | ‒ | ‒ |
25 | ‒ | ‒ | ‒ | ● | ‒ | ‒ | ‒ |
30 | ‒ | ‒ | ‒ | ‒ | ● | ‒ | ‒ |
40 | ‒ | ‒ | ‒ | ‒ | ‒ | ● | ‒ |
50 | ‒ | ‒ | ‒ | ‒ | ‒ | ‒ | ● |
●
available size
**Shaft and support rail units TS and shaft diameter dLw: see Catalogue WF 1, Shaft Guidance Systems.
Design and safety guidelines
Adjacent construction for non-locating bearing track rollers
For non-locating bearing track rollers without an inner ring, the rolling element raceway on the shaft must be hardened and ground. The surface hardness must be 670 HV + 170 HV. The hardening depth CHD or SHD must be sufficiently large.
Tolerances and surface data for the shaft raceway
Design of the shaft: see table .
Diameter tolerance of shafts | Roughness | Roundness | Parallelism | |
---|---|---|---|---|
without | with | max. | max. | max. |
k5 | g6 | Ra 0,4 (Rz 2) | 25% | 50% |